How to implement asset tracking software in the factory environment, what you need to know first?
22/Mar/2024
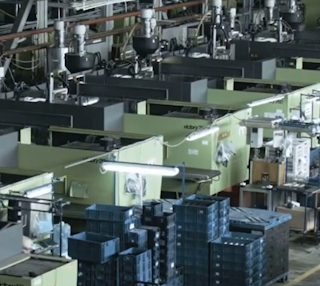 Introduction
Implementing asset tracking software in a manufacturing environment can significantly improve operational efficiency and help manage resources effectively. Here's a general guide on how to implement asset tracking software:
Assess Your Needs: Understand what assets you need to track. These could include machinery, tools, vehicles, raw materials, finished products, etc. Identify the key information you want to track about each asset, such as location, condition, maintenance history, etc.
Choose the Right Software: Research and select asset tracking software that meets your specific requirements. Look for features like barcode/RFID scanning, real-time tracking, integration capabilities with existing systems (such as ERP or CMMS), reporting and analytics, mobile accessibility, and scalability.
Data Collection and Tagging: Assign unique identifiers (barcodes, QR codes, RFID tags) to each asset. Capture relevant data about each asset, such as serial numbers, purchase date, warranty information, maintenance schedules, etc. This data can be entered manually or imported from existing databases. If you plan to use RFID technology, 1 object 1 identity is a must for RFID implementation.
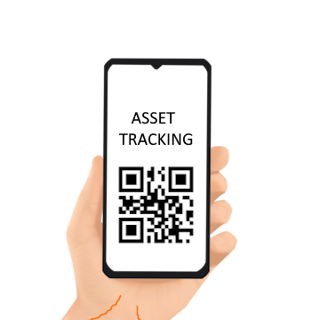 Install Hardware (if necessary): Depending on the chosen tracking technology (barcode scanners, RFID readers), install necessary hardware in your facility. Ensure that the hardware is compatible with your chosen software.
Training: Train employees on how to use the asset tracking software and associated hardware. Provide instructions on how to scan assets, update information, perform audits, and troubleshoot common issues.
Integration: Integrate the asset tracking software with other relevant systems in your manufacturing environment, such as inventory management, maintenance management, or procurement systems. This ensures seamless data flow and eliminates duplication of efforts.
Pilot Testing: Conduct a pilot test of the asset tracking system in a small area or department to identify any issues and refine processes before full implementation.
Rollout and Implementation: Once the pilot test is successful, roll out the asset tracking system across the entire manufacturing facility. Communicate the changes to all stakeholders and provide ongoing support as needed.
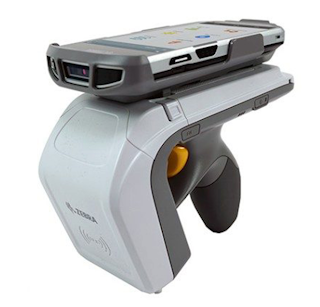 Regular Maintenance and Updates: Schedule regular maintenance for both software and hardware components to ensure optimal performance. Keep the software up-to-date with the latest patches and updates to address security vulnerabilities and add new features.
Continuous Improvement: Continuously monitor and evaluate the effectiveness of the asset tracking system. Solicit feedback from users and identify areas for improvement. Adjust processes and procedures as needed to optimize asset utilization and minimize downtime.
Summaries
By following these steps, you can successfully implement asset tracking software in your manufacturing environment and reap the benefits of improved visibility, efficiency, and productivity.
|